Top Manufacturers:
Branson - Dukane - Crest Ultrasonic - Herrmann - Mecasonic - Genesis - Telsonic
We are a component-level repair facility
Find Out MoreWe repair unsupported legacy equipment
Find Out MoreView some of the highly-specialized Ultrasonic Welder Repair Services we offer
Rochester Industrial Services is perfectly positioned to provide quick, affordable repairs for your ultrasonic welder. We cover all types of ultrasonic welding including plastic welding, and synthetic / textile bonding. Even if you have obscure or off-brand ultrasonic equipment, chances are we can help no matter what manufacturer or model you have. If you're looking for service, repair, or maintenance on any items not mentioned below, please contact us through any of the various means available or use our online form to inquire.
Problem: You Have Critical Equipment Down
Your worst nightmare: Ultrasonic welding equipment failures that bring production to a grinding halt.
Solution: Rochester Industrial Services Can Fix It Now!
Our quick, component-level industrial electronic repair processes, procedures, and outcomes are the best...
- Priority repairs put the process in motion for a quick turnaround for critical "line down" situations
- Your equipment stays on the repair bench until the repair is completed
- In most cases we turn your product around and ship it back the same day
- Our diverse, forty-six-year ultrasonic repair experience gives us the expertise to service your ultrasonic welding equipment like no one else can
- Our repair expertise combined with full test equipment and stands covers all the bases
- Our unique process and cutting-edge repair industry procedures set the standard
- From plastic welders and rubber slitters, to spin welders and ultrasonic cleaners – we cover ALL manufacturers and models of industrial ultrasonic equipment
- We are a component-level repair facility
- Hundreds of loyal repeat customers agree that our repair performance and outcomes rank among the best in the country
- 100% customer satisfaction is our goal
Why should you choose Rochester Industrial Services for your industrial ultrasonic welder equipment and ultrasonic cleaner equipment?
Our repair process covers the entire unit, not just fixing what has failed. All failed and high-probability-of-failure components are replaced – before they fail and bring your production line to a grinding halt!
All refurbished merchandise we offer for sale undergoes the same rigorous evaluation and repair process. Our preemptive approach keeps failures in the field low and customer satisfaction high. And there's more...
Obsolete or No Longer Supported by the OEM?
900 Series Branson Welders? No Problem! Find Out More
Why ship Herrmann or Mecasonic welders overseas for service?
We support all models in the United States!
Next day repairs possible!
Ultrasonic Welder Repairs by Rochester Industrial Services, Inc.
Industrial Ultrasonic Repair is our specialty! We have Test Fixtures!
ALL Manufacturers of Ultrasonic Welders and Cleaners Repaired or Refurbished
Branson - Dukane - Crest Ultrasonic - Herrmann - Mecasonic - Genesis
We have repaired or refurbished ultrasonic welders, cleaners from numerous domestic and foreign manufacturers - View List
Ultrasonic Converter: Exploded View
Ultrasonic Welder Repair Services
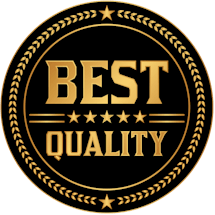
BEST Warranty - RIS Fair & Honest 1-Year Warranty included
FREE Evaluation - We offer FREE same-day evaluation
FREE Support - We offer FREE telephone tech support
Ready to Ship It In for repair? Use our Ship It Now form
Not just a Band-Aid® – We give you the works!
Instead of the "Band Aid®" approach others use, our process includes:
Actuator / Thruster Assembly
- Full power-up evaluation / failure verification prior to disassembly
- Each Unit is fully disassembled and cleaned
- Mechanical operation is inspected; all failed and questionable components are replaced as needed
- Pneumatic System / Hydraulic System is serviced including replacement of lines, fittings, gauges, and regulators as needed
- Electrical and electronic components and circuits are serviced as needed
- Reassembled and returned to original manufacturer's specifications
- Full system load testing
- The entire unit is serviced and tested
- Full 1-year warranty
Power Supply / Control Unit
- Full power-up evaluation / failure verification prior to disassembly
- Power Supply / Control Unit is fully disassembled and cleaned
- Front Control Panel is inspected and refurbished as needed, including video displays, output controls, push buttons, and switches
- Main Power Board will have all critical electronic components replaced
- Interface Boards and cables will be inspected and serviced as needed
- Cooling Fans and filters are replaced as standard procedure.
- Burn in cycling, load testing, and output verification are all included in the final stages of our service.
- Full 1-year warranty
Converters / Transducers
- We specialize in converter and tooling rebuild and testing, providing assurance that your complete stack is tested and verified 100% and can be tuned to the proper frequency, reducing system failures and down time.
- We have the equipment and experience to fully test all converters, boosters, and tooling 100%
- Custom one of a kind units
- Preventive maintenance programs
Complete Ultrasonic Systems
- Forward thinking approach is provided for all our customers.
- No charge telephone and email support as needed prior to your system failing
- Choosing us has proven to be the answer!
- We provide you with the information you need on system applications, and preventive maintenance that others refuse to share.
- We are not just a repair facility, but your partner.
- Let us work for you!
- Full in-process repair data with photographic archiving that tracks and stores information on your unit from start to finish